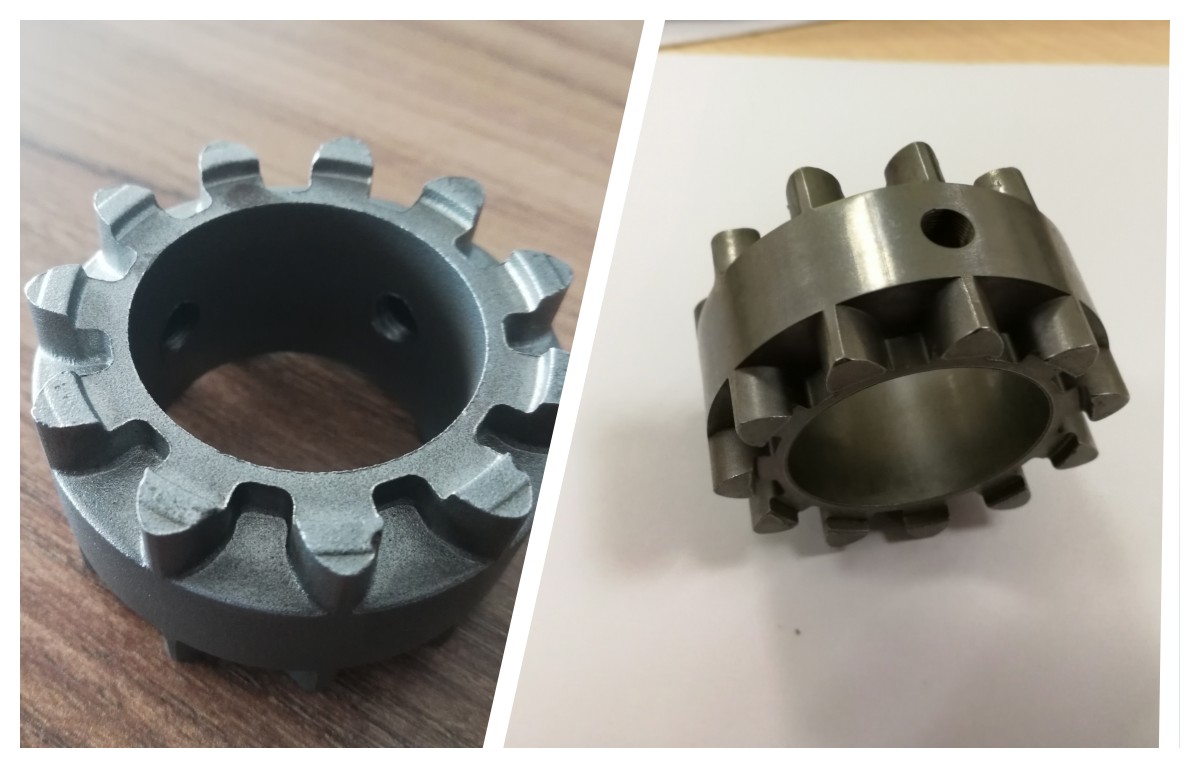
Switching from casting parts to powder metallurgy (PM) parts can offer several key advantages, depending on the application. Here are some reasons why a company or engineer might choose to replace casting with powder metallurgy:
1. Improved Material Properties
- Higher Precision: PM parts can be produced with tighter tolerances, reducing the need for extensive machining.
- Material Utilization: Powder metallurgy produces less waste compared to casting because it uses almost all the material, whereas casting results in some material loss during the process.
- Enhanced Strength: PM parts can exhibit better mechanical properties, such as higher strength and wear resistance, because of the uniformity of the microstructure achieved during sintering.
2. Cost Efficiency
- Lower Labor Costs: Powder metallurgy typically requires less post-processing and fewer complex operations compared to casting, making it more cost-effective for mass production.
- Reduced Material Waste: Since PM uses powdered metal, excess material is minimized, leading to a more efficient use of resources and potentially lowering the cost of raw materials.
3. Complex Geometries and Fine Features
- PM is capable of producing parts with complex shapes, which might be challenging or expensive to achieve with casting. Features like internal channels, intricate geometries, and fine details can often be manufactured directly in PM, reducing the need for secondary operations.
4. Consistency and Reproducibility
- Uniformity: The sintering process in PM ensures that each part has a uniform material structure, which is harder to achieve with casting, especially with more complex alloys.
- High Volume Production: For high-volume production, PM offers consistent quality with minimal variation across parts, something that can be challenging with traditional casting methods.
5. Reduced Need for Secondary Operations
- Many PM parts require little to no further machining, especially for certain shapes and tolerances. In contrast, casting often requires additional operations like trimming, cleaning, and machining to achieve the desired finish and accuracy.
6. Reduced Porosity and Enhanced Surface Quality
- PM parts can have lower porosity compared to cast parts, which can lead to better performance, particularly in applications that require high integrity or load-bearing capabilities.
7. Better Control Over Alloy Composition
- Powder metallurgy allows for precise control over the material composition and can easily accommodate different alloying elements. This allows manufacturers to fine-tune the material properties to meet specific needs for the application, something that can be more difficult or costly with casting.
8. Sustainability
- Powder metallurgy often uses recycled powders and has less material waste compared to casting processes. This makes it a more environmentally friendly option in terms of raw material usage and energy consumption.
9. Lighter Parts
- PM can be used to produce parts with optimal material distribution, leading to lighter components without sacrificing strength. This is particularly useful in industries like automotive or aerospace, where weight reduction is critical.
10. Customization of Parts
- Because the powder metallurgy process is flexible, manufacturers can easily adjust and customize parts for specific requirements, whether in terms of material, shape, or other attributes.
When Might Casting Be a Better Option?
While powder metallurgy has many advantages, there are scenarios where casting might be preferred, such as:
- Large and Complex Parts: For very large parts or parts with highly intricate features, casting might be more practical.
- Low-Cost for Simple Parts: For simpler, lower-volume parts, casting might be more cost-effective.
- Parts with High Ductility: Certain casting alloys can have better ductility or elongation than PM alloys, depending on the application.
Ultimately, the choice between casting and powder metallurgy depends on factors like part design, production volume, material requirements, and cost constraints.